A discussion on how the latest data analysis platforms bring operational technology benefits to the edge for real-time insights in manufacturing.
Listen
to the podcast. Find it on iTunes. Download the transcript. Sponsor: Hewlett Packard Enterprise.
Dana Gardner:
Hello, and welcome to the next edition of the BriefingsDirect Voice of the
Customer podcast series. I’m Dana
Gardner, Principal Analyst at Interarbor
Solutions, your host and moderator for this ongoing discussion on digital transformation
success stories.
![]() |
Gardner |
Our next edge computing trends
discussion explores the rapidly evolving confluence of operational
technology (OT) and Internet of Things
(IoT). New advances in data processing, real-time analytics, and platform
efficiency have prompted innovative and impactful OT approaches at the edge.
We’ll now hear how such data
analysis platforms bring manufacturers data-center caliber benefits for real-time
insights where they are needed most.
To hear more about the latest
capabilities in gaining unprecedented operational insights, please join me in
welcoming Riaan
Lourens, Vice President of Technology in the Office of the Chief Technology
Officer at PTC. Welcome, Riaan.
Riaan Lourens: Hey,
Dana. Thanks for having me.
Gardner: We are also here with Tripp Partain, Chief Technology Officer of IoT Solutions at Hewlett Packard Enterprise (HPE). Welcome, Tripp.
Tripp Partain: Hey,
Dana. Thanks a lot. I appreciate the opportunity.
Gardner: Riaan,
what kinds of new insights are manufacturers seeking into how their operations
perform?
![]() |
Lourens |
Lourens: We
are in the midst of a Fourth
Industrial Revolution, which is really an extension of the third, where we used
electronics and IT to automate manufacturing. Now, the fourth is the digital
revolution, a fusion of technology and capabilities that blur the lines
between the physical and digital worlds.
With the influx of these technologies,
both hardware and software, our customers -- and manufacturing as a whole, as
well as the discrete process industries -- are finding opportunities to either
save or make more money. The trend is focused on looking at technology as a business
strategy, as opposed to just pure IT operations.
Digital revolution in business
There are
a number of examples of how our customers have leveraged technology to drive their
business strategy.
Gardner: Are
we entering a golden age by combining what OT and IT have matured into over the
past couple of decades? If we call this Industrial Revolution 4.0,
(I4.0) there must be some kind of major opportunities right now.
Lourens: There
are a lot of initiatives out there, whether it’s I4.0, Made in China 2025,
or the Smart
Factory Initiative in the US. By democratizing the process of providing value
-- be it with cloud capabilities, edge computing, or anything in between – we
are inherently providing options for manufacturers to solve problems that they were
not able to solve before.
The
opportunity for manufacturers today allows them to solve problems that they face almost immediately. There is quick time-to-value by leveraging technology that is consumable.
If you look at it from a broader technology standpoint, in the past we had very large, monolith-like deployments of technology. If you look at it from the ISA-95 model, like Level 3 or Level 4, your MES deployments or large-scale enterprise resource planning (ERP), those were very large deployments that took many years. And the return on investment (ROI) the manufacturers saw would potentially pay off over many years.
The opportunity that exists
for manufacturers today, however, allows them to solve problems that they face
almost immediately. There is quick time-to-value by leveraging technology that
is consumable. Then they can lift and drop and so scale [those new solutions] across
the enterprise. That does make this an era the likes of which nobody has seen
before.
Gardner:
Tripp, do you agree that we are in a golden age here? It seems to me that we
are able to both accommodate a great deal of diversity and heterogeneity of the
edge, across all sorts of endpoints and sensors, but also bring that into a
common-platform approach. We get the best of efficiency and automation.
Partain: There
is a combination of two things. One, due to the smartphone evolution over the
last 10 years, the types of sensors and chips that have been created to drive that
at the consumer level are now at such reasonable price points you are able to apply
these to industrial areas.
![]() |
Partain |
To Riaan’s point, the price
points of these technologies have gotten really low -- but the capabilities are
really high. A lot of existing equipment in a manufacturing environment that
might have 20 or 30 years of life left can be retrofitted with these sensors
and capabilities to give insights and compute capabilities at the edge. The
capability to interact in real-time with those sensors provides platforms that didn’t
exist even five years ago. That combines with the right software capabilities so
that manufacturers and industrials get insights that they never had before into
their processes.
Gardner: How
is the partnership between PTC
and HPE taking advantage of this new opportunity? It seems you are coming
from different vantage points but reinforcing one another. How is the whole
greater than the sum of the parts when it comes to the partnership?
Partnership for progress, flexibility
Lourens: For
some context, PTC is a software vendor. Over the last 30 years we targeted our
efforts at helping manufacturers either engineer software with computer-aided
design (CAD) or product lifecycle management (PLM). We have evolved to our growth
areas today of IoT solution platforms and augmented reality (AR)
capabilities.
The challenge that
manufacturers face today is not just a software problem. It requires a robust ecosystem
of hardware vendors, software vendors, and solutions partners, such as regional
or global systems integrators.
The reason we
work very closely with HPE as an alliance partner is because HPE is a
leader in the space. HPE has a strong offering of
compute capabilities -- from very small gateway-level compute all the way through
to hybrid technologies
and converged
infrastructure technologies.
Ultimately our customers need flexible options
to deploy software at the right place, at the right time, and throughout
any part of their network. We find that HPE is a strong partner on this front.
Gardner:
Tripp, not only do we have lower cost and higher capability at the edge, we
also have a continuum of hybrid IT. We can use on-premises micro-datacenters,
converged infrastructure, private cloud, and public cloud options to choose
from. Why is that also accelerating the benefits for manufacturers? Why is a continuum
of hybrid IT – edge to cloud -- an important factor?
Partain: That
flexibility is required if you look at the industrial environments where these
problems are occurring for our joint customers. If you look at any given
product line where manufacturing takes place -- no two regions are the same and
no two factories are the same. Even within a factory, a lot of times, no two production
lines are the same.
There is a wide diversity in how manufacturing takes place. You need to be able to meet those challenge with the customers to give them the deployment options that meet each of those environments.
It’s interesting. Factories don’t
do enterprise IT-like deployments, where every factory takes on new
capabilities at the same time. It’s much more balanced in the way that products
are made. You have to be able to have that same level of flexibility in how you
deploy the solutions, to allow it to be absorbed the same way the factories do
all of their other types of processes.
We have seen the need for different
levels of IT to match up to the way they are implemented in different types of
factories. That flexibility meets them where they are and allows them to get to
the value much quicker -- and not wait for some huge enterprise rollout, like what
Riaan described earlier with ERP systems that take multiple years.
By leveraging new, hybrid, converged,
and flexible environments, we allow a single plant to deploy multiple solutions
and get results much quicker. We can also still work that into an enterprise-wide
deployment -- and get a better balance between time and return.
Gardner: Riaan,
you earlier mentioned democratization. That jumped out at me. How are we
able to take these advances in systems, software, and access and availability
of deployments and make that consumable by people who are not data scientists? How
are we able to take the results of what the technology does and make it
actionable, even using things like AR?
Lourens: As
Tripp described, every manufacturing facility is different. There are typically
different line configurations, different programmable logic controller (PLC)
configurations, different heterogeneous systems -- be it legacy IT systems or homegrown
systems -- so the ability to leverage what is there is inherently important.
From a strategic perspective, PTC
has two core platforms; one being our ThingWorx Platform
that allows you to source data and information from existing systems that are
there, as well as from assets directly via the PLC or by embedding software
into machines.
We also have the ability to simplify
and contextualize all of that information and make sense of it. We can then drive
analytical insights out of the data that we now have access to. Ultimately we
can orchestrate with end users in their different personas – be that the
maintenance operator, supervisor, or plant manager -- enabling and engaging
with these different users through AR.
Four capabilities for value
There are
four capabilities that allow you to derive value. Ultimately our strategy is to
bring that up a level and to provide capabilities
solutions to our end customers across four different areas.

So across those four solution
areas we can apply our technology together with that of our sourced partners.
We allow our customers to find use-cases within those four solution areas that
provides them a return on investment.
One example of that would be
leveraging augmented work instructions. So instead of an operator going through
a maintenance procedure by opening a folder of hundreds of pages of
instructions, they can leverage new technology such as AR to guide the operator
in process, and in situ, in terms of how to do something.
There are many use cases
across those four solution areas that leverage the core capabilities across the
IoT platform, ThingWorx, as well as the AR platform, Vuforia.
Gardner: Tripp, it sounds like we are taking the best of what people can do and the best of what systems and analytics can do. We also move from batch processing to real time. We have location-based services so we can tell where things and people are in new ways. And then we empower people in ways that we hadn’t done before, such as AR.
Are we at the point where
we’re combining the best of cognitive human capabilities and machine
capabilities?
Partain: I
don’t know if we have gotten to the best yet, but probably the best of what
we’ve had so far. As we continue to evolve these technologies and find new ways
to look at problems with different technology -- it will continue to evolve.
We are getting to the new
sweet spot, if you will, of putting the two together and being able to drive
advancements forward. One of the things that’s critical has to do with where
our current workforce is.
A number of manufacturers I
talk to -- and I’ve heard similar from PTC’s customers and our joint customers --
is you are at a tipping point in terms of the current talent pool, with those
currently employed and those getting close to retirement age.
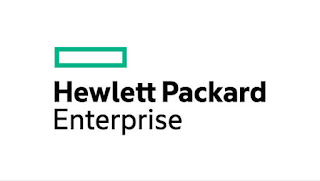
The solutions are now
available to really enhance those jobs. We are starting to see all of the
pieces come together. That’s where both IoT solutions -- but even especially AR
solutions like PTC Vuforia -- really come into play.
Gardner:
Riaan, in a large manufacturing environment, only small iterative improvements
can make a big impact on the economics, the bottom line. What sort of future
categorical improvements value are we looking at? To what degree do we have an
opportunity to make manufacturing more efficient, more productive, more
economically powerful?
Tech bridges skills gap, talent shortage
Lourens: If
you look at it from the angle that Tripp just referred to, there are a number
of increasing pressures across the board in the industrial markets via the
workers’ skills gap. Products are also becoming more complex. Workspaces are
becoming more complex. There are also increasing customer demands and
expectations. Markets are just becoming more fiercely competitive.
But if you leverage
capabilities such as AR -- which provides augmented 3-D work instructions, expert
guidance, and remote assistance, training, and demonstrations -- that’s one
area. If you combine that, to Tripp’s point, with the new IoT capabilities, then
I think you can look at improvements such as reducing
waste in processes and materials.
We have seen customers reducing by 30 percent unplanned downtime, which is a very common use case that we see manufacturers target. We also see reducing energy consumption by 3 to 7 percent. And we're looking at improving productivity by 20 to 30 percent.
We have seen customers reducing by 30 percent unplanned downtime, which is a very common use case that we see manufacturers target. We also see reducing energy consumption by 3 to 7 percent at a very large ship manufacturer, a customer of PTC’s. And we’re generally looking at improving productivity by 20 to 30 percent.
By leveraging this technology
in a meaningful way to get iterative improvements, you can then scale it across
the enterprise very rapidly, and multiple use cases can become part of the solution.
In these areas of opportunity, very rapidly you get that ROI.
Gardner: Do we
have concrete examples to help illustrate how those general productivity
benefits come about?
Joint solutions reduce manufacturing pains
Lourens: A
joint-customer between HPE and PTC focuses on manufacturing and distributing
reusable and recyclable food packaging containers. The company, CuBE
Packaging Solutions, targeted protective maintenance in manufacturing. Their
goal is to have the equipment notify them when attention is needed. That allows
them to service what they need when they need to and focus on reducing
unplanned downtime.
In this particular example,
there are a number of technologies that play across both of our two companies. The
HPE Nimble Storage
capability and HPE Synergy
technology were leveraged, as well as a whole variety of HPE Aruba
switches and wireless access points, along with PTC’s ThingWorx solution
platform.
The CuBE Packaging solution ultimately was pulled together through an ecosystem partner, Callisto Integration, which we both worked with very closely. In this use case, we not only targeted the plastic molding assets that they were monitoring, but the peripheral equipment, such as cooling and air systems, that may impact their operations. The goal is to avoid anything that could pause their injection molding equipment and plants.
Gardner:
Tripp, any examples of use-cases that come to your mind that illustrate the
impact?
Partain: Another
joint-customer that comes to mind is Texmark
Chemicals in Galena Park, Texas. They are
using number of HPE solutions, including HPE Edgeline,
our micro-datacenter. They are also using PTC ThingWorx and a number of other
solutions.
They have very large pumps
critical to the operation as they move chemicals and fluids in various stages
around their plant in the refining process. Being able to monitor those in real
time, predict potential failures before they happen, and use a combination of
live data and algorithms to predict wear and tear, allows them to determine the
optimal time to make replacements and minimize downtime.
Such uses cases are one of the
advantages when customers come and visit our IoT Lab in
Houston. From an HPE standpoint, not only do they see our joint solutions in
the lab, but we can actually take them out to the Texmark location and Texmark
will host and allow you them see these technologies in real-time working at
their facility.
Similar as Riaan mentioned, we
started at Texmark with condition monitoring and now the solutions have moved
into additional use cases -- whether it’s mechanical integrity, video as a sensor,
and employee-safety-related use cases.
We started with condition
monitoring, proved that out, got the technology working, then took that
framework -- including best-in-class hardware and software -- and continued to
build and evolve on top of that to solve expanded problems. Texmark has been a
great joint customer for us.
Gardner:
Riaan, when organizations hear about these technologies and the opportunity for
some very significant productivity benefits, when they understand that
more-and-more of their organization is going to be data-driven and real-time
analysis benefits could be delivered to people in their actionable context,
perhaps using such things as AR, what should they be doing now to get ready?
Start small
Lourens: Over
the last eight years of working with ThingWorx, I have noticed the initial
trend of looking at the technology versus looking at specific use-cases that
provide real business value, and of working backward from the business value.
My recommendation is to target
use cases that provide quick time-to-value. Apply the technology in a way that
allows you to start small, and then iterate from there, versus trying to prove
your ROI based on the core technology capabilities.
Ultimately understand the
business challenges and how you can grow your top line or your bottom line.
Then work backward from there, starting small by looking at a plant or
operations within a plant, and then apply the technology across more people. That
helps create a smart connected people strategy. Apply technology in terms of
the process and then relative to actual machines within that process in a way
that’s relevant to use cases -- that’s going to drive some ROI.
Gardner:
Tripp, what should the IT organization be newly thinking? Now, they are tasked
with maintaining systems across a continuum of cloud-to-edge. They are seeing
micro-datacenters at the edge; they’re doing combinations of data-driven
analytics and software that leads to new interfaces such as AR.
How should the IT organization
prepare itself to take on what goes into any nook and cranny in almost any
manufacturing environment?
IT has to extend its reach
Partain: It’s
about doing all of that IT in places where typically IT has had a little or no
involvement. In many industrial and manufacturer organizations, as we go in and
start having conversations, IT really has usually stopped at the datacenter back-end.
Now there’s lots of technology in the manufacturing side, too, but it has not typically
involved the IT department.
One of the first steps is to
get educated on the new edge technologies and how they fit into the overall
architecture. They need to have the existing support frameworks and models in
place that are instantly usable, but also work with the business side and frame-up
the problems they are trying to solve.
As Riaan mentioned, being able
to say, “Hey, here are the types of technologies we in IT can apply to this
that you [OT] guys haven’t necessarily looked at before. Here’s the
standardization we can help bring so we don’t end up with something completely
different in every factory, which runs up your overall cost to support and run.”
It’s a new world. And IT is going
to have to spend much more time with the part of the business they have
probably spent the least amount of time with. IT needs to get involved as early
as possible in understanding what the business challenges are and getting
educated on these newer IoT, AR, virtual reality (VR), and edge-based solutions.
These are becoming the extension points of traditional technology and are the new
ways of solving problems.
Gardner: I’m
afraid we’ll have to leave it there. We have been discussing the rapidly
evolving confluence of OT and the IoT. And we have learned how data processing,
real-time analytics, and platform efficiency are all prompting new OT
approaches at the very edge of manufacturing.
Please join me in thanking our
guests, Riaan Lourens, Vice President of Technology in the office of the CTO at
PTC. Thank you so much, Riaan.
Lourens:
Thanks for having me, Dana. It’s been a pleasure.
Gardner: And
we have also been joined by Tripp Partain, Chief Technology Officer of IoT
Solutions at HPE. Thank you so much, Tripp.
Partain: Yes, I
enjoyed it. Thank you very much.
Gardner: And a big thank you to our audience as well for joining this BriefingsDirect Voice of the Customer digital transformation success story discussion. I’m Dana Gardner, Principal Analyst at Interarbor Solutions, your host for this ongoing series of Hewlett Packard Enterprise-sponsored interviews.
Thanks again for listening,
please pass this along to your IT community, and do come back next time.
Listen
to the podcast. Find it on iTunes. Download the transcript. Sponsor: Hewlett Packard Enterprise.
A discussion how the latest data analysis platforms bring
operational technology benefits to the edge for real-time insights in manufacturing.
Copyright Interarbor Solutions, LLC, 2005-2019. All rights reserved.
You may also be
interested in:
- How rapid machine learning at the racing edge accelerates Venturi Formula E Team to top-efficiency wins
- The budding storage relationship between HPE and Cohesity brings the best of startup innovation to global enterprise reach
- Industrial-strength wearables combine with collaboration cloud to bring anywhere expertise to intelligent-edge work
- HPE’s Erik Vogel on what's driving success in hybrid cloud adoption and optimization
- IT kit sustainability: A business advantage and balm for the planet
- How total deployment intelligence overcomes the growing complexity of multicloud management
- Manufacturer gains advantage by expanding IoT footprint from many machines to many insights
- How Texmark Chemicals pursues analysis-rich, IoT-pervasive path to the ‘refinery of the future’
- Using AI to Solve Data and IT Complexity--And Better Enable AI